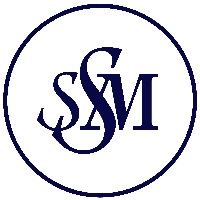
Steamship Mutual
Published: November 08, 2017
January 2008
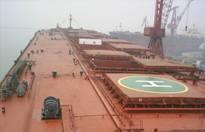
Background
With the IMO requirement for single hull tankers to be phased out by 2010 approaching, the options available to the owner of these older vessels are limited. Previously it was thought that these vessels would either be converted to double hull, scrapped, or some being converted into Floating Production Storage Offloading units.
However, in light of the high charter rates being achieved by bulk carriers many shipowners are now looking at the cheaper option (due to reduced shipyard time and less new steel required) of converting their VLCCs into Very Large Ore Carriers. Approximately 30 single hulled VLCCs are presently destined to be converted.
The conversion generally takes 3 to 6 months in the shipyard, this process adding another 10 to 14 years to the life of a vessel. This compares favourably with the 4 year wait for delivery of a new bulk carrier, even if yard capacity can be obtained.
The attraction for owners of sending their VLCC’s for conversion is easily seen when the cost of converting a VLCC will generally be paid off in 1 to 2 years at present charter rates and with a bullish outlook for the dry bulk market. However, the impact on charter rates of the influx of over 550 capesize bulkcarriers, due to be delievered over the next five years, remains to be seen.
Generally, these vessels will be larger than the traditional capesize bulkcarrier (140-200,000 dwt) at 230-300,000 dwt and are intended for the Brazil and South Africa to China trade to satisfy China’s prodigous requirements for iron ore.
Structural Changes to the Hull
The converstion from VLCC to VLOC necessitates several structural changes to the vessel. The VLOC uses only the original 5 or 6 centre tanks of the VLCC to carry the ore cargo, while the side tanks remain mostly unchanged and used purely for the carriage of ballast. However due to the excessive ballast capacity now available in the side tanks, some of these tanks, possibly including the slop tanks, may be changed to void spaces. Due to the limited number of holds, as opposed to the nine holds typically found on a capesize, high density cargoes will have to be carried as a homogenous load. To facilitate the use of the centre tanks holes are cut in the main deck to fit suitably sized hatch coamings with side rolling hatch covers. The loss of longitudinal strength caused by loss of deck plating and associated underdeck framing is addressed by fitting saddle tanks under the deck extending from the longitudinal bulkhead between the centre and side tank, to under the hatch coaming to provide support for the hatch coaming/hatch cover arrangement. Due to the large ballast capacity already available in the side tanks, the saddle tanks are usually fitted as voids.
In order for the vessel to handle the large loadings imposed on the bottom plating by ore cargoes (for a 280-300,000 dwt vessel this will be up to 70,000t per hold) in each hold a substantial void inner/double bottom is built into the centre tank, with the transverse web frames which characterised the framing system of the tanker being cut back level with the new tank top. The centreline girder is modified and additional longitudinal side girders are fitted between the centreline and the longitudinal bulkheads. Crucially, the inner bottom web frames and additional intermediate floors fitted transversely between the existing transverse webs have to be continuous passing through the port and starboard longitudinal bulkheads into the side tanks to avoid tearing of these bulkheads; as with either the hold full and the tanks empty or vice versa finite element analysis has shown these areas to be critical due to the loadings imposed. The new intermediate floors are extended into the wing tanks for a number of metres and finished with scarphing brackets. The web frames within the side tanks may also require increasing in area such that the openings in the webs are reduced to cope with the new loading regime.
The horizontal framing fitted to the transverse bulkheads of the centre tanks gives rise to the problem of cargo entrapment on the frames. Depending on the design of the bulkhead this may be on one or both sides of the bulkhead. This problem is avoided by the fitting of shedder plates between frame edge and bulkhead at an appropriate angle to allow cargo to slide off to the hold floor. Due to the increased weight this causes on the transverse bulkheads the framing at the base of the bulkhead is increased and faired with a more substantial stool. On some designs hopper plates are fitted to the longitudinal bulkheads as would be found on a conventional bulk carrier, however on other designs on the port and starboard side of the hold the join between bulkhead and new inner bottom is square, there are no hopper plates or tank bulkhead as found in a traditional bulk carrier to move the cargo towards the centre of the hold. Therefore the emptying of the hold will require more use of prime movers to shift the cargo from dead areas out of reach of the grab to under the hatch square.
So far as possible existing ballast and cargo oil piping may be used for the new ballasting arrangements, however, in order to cope with the loading rates which may be experienced, the ballast pumping capacity may need to be increased by up to 50%.
Additional modifications to the new holds will be the fitting of suitable access ladders to the tank top in line with Means of Access Regulations. Also suitable bilges, alarms and pumping arrangements would have to be installed in line with statutory requirements. In addition, the Oil Fuel Tank Potection Regulations under MARPOL Annex 1 will be applicable as it will be a major conversion, necessitating a double bottom or double skin to be built in to fuel tanks bounded by the shell plating; dependending on the tanks capacity. Also, the fixed fire fighting monitors on the main deck may be retained for deck cleaning, but if hazardous cargoes are to be carried then a fixed CO2 system will need to be fitted to service the holds. If the vessel has steam powered deck machinery thought will have to be given to possibly changing to electric or electro hydraulic machinery for reasons of economy. Another option is the fitting of a smaller boiler and decommisioning the main boilers and utlislising the existing deck machinery.
The change from VLCC to VLOC gives rises to an appoximate weight gain of 6,000t, consisting of additional centre tank steelwork, hatch coamings and covers. Approximately 1,500t is lost due to cropping down of the transverse web frames in the centre tanks, cutting of hatch openings in the main deck, removal of pipe work, and removal of other deck fittings such as tank lids, IG deck fittings, p-v valves, hose handling lifting appliances etc. The net result being an increase in lightship displacement of 4,500t for an average VLCC to VLOC conversion, and a corresponding drop in deadweight.
Statutory Requirements
The change from a tanker to a bulkcarrier gives rise to compliance issues with a number of statutory requirements. The principal change is from a type A vessel to a type B vessel under the Load Line Convention and due to the vessel lifting a similar weight of cargo as to when she was a VLCC the waterline will be similar to previously. This give rise to issues with the minimum bow height and reserve buoyancy forward.
This can be overcome by fitting a raised forecastle, which in itself is no easy task allowing for the modifications to the chain lockers and lifting the windlass, mooring winches and mooring furniture by a deck. A further complication can be that the raising of the forecastle interfers with the IMO visibility requirements from the bridge looking past the forecastle, this may also require an increase in the height of the bridge to ensure the visibility past the forecastle is kept within requirements. The class requirements for the fitting of raised forecastles on bulk carriers, OBO’s and OO’s does not seem to apply, as the Class requirement makes no mention of conversions post the date of implementation.
Class Requirements
It seems that issues with regards to Class and its application to the conversion of VLOC’s into VLCC’s is still being fine tuned, however, the following points give some indicaiton of the areas of concern:
- Class would treat such a conversion as a substantial or major conversion, with the main concern being that the strength of the new hull has been carefully considered, with a finite element analysis required to be conducted of the new VLOC mid hull section.
- The Class requirements for bulk carriers would apply to the conversion, however, it would seem that these are dependent on the Class notations which the owner requires.
- The Class requirements for the strength and securing of small hatches on exposed fore decks, strength requirements for fore deck fittings and the evaluation of scantlings for hatch covers and coamings would all apply to the converstion.
- It seems that Common Structural Rules for bulk carriers or tankers would not be applied, as class consider it would be impractical to apply these to an existing ship.
- Due to the change in vessel type the following documentation would also be required to be generated and provided for the new hull structure:
1. Loading booklet (longitudinal strength and intact stability).
2. Damage stability.