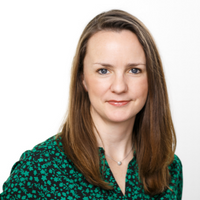
Heloise Campbell
Published: September 21, 2017
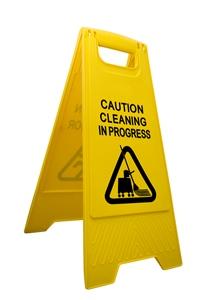
Hold cleaning disputes are not infrequent and can result in the need for multiple surveys and significant delays and costs. This article discusses some of the practical aspects of cleaning cargo holds, including the factors which will be relevant to the extent of cleaning required, and also how appropriate systems can be put into place to carry this out in an efficient manner. It also comments on a recent London arbitration which considered an implied term in relation to the standard of cleanliness required and whether charterparty requirements were met in circumstances where there were contradictory survey results.
Introduction to Hold Cleaning
Preparation of cargo holds for the next cargo is an important operational consideration on all bulk carriers. If not properly planned and carried out inadequate hold cleaning can lead to several different claim types. Claims in respect of the cargo, such as for shortage, contamination or water damage, can be directly linked to the hold cleaning, in addition to which charterparty disputes resulting from delays and berth costs may arise. By way of an example, unless the hatch cover seating surfaces are clean, a weathertight seal will not be possible resulting in a risk of water accumulating and dripping into the hold and causing cargo damage.
The extent of hold cleaning and preparation required for the next cargo will depend on several factors; most importantly, the cargo to be loaded and its intended use. In the bulk carrier trade a number of terms are often used to describe the cleanliness requirements but Members should be aware that there is no universal definition of these terms and very often surveyors will inspect holds subjectively based purely on their previous experiences rather than set criteria. ‘Standards’ such as ‘hospital’, ‘ grain’, ‘normal’ and ‘shovel’ are all in common use and are often included in charterparties. However, even when one of these commonly used terms is used, disputes can arise in relation to the cleaning standard required as some countries interpret the requirements differently and what may be acceptable as ‘grain clean’ in one port may not be acceptable in another. For instance, it is well known that Australia, USA and Canada require very high standards of hold cleanliness prior to loading grain cargoes.
A broad guide to these commonly used terms is:
“Hospital Clean” is the most stringent and requires all hold surfaces to have 100% intact paint coatings on all surfaces (including the tank top, all ladder rungs and undersides of hatches).
“Grain Clean” requires the holds to be free from insects, odour, residue of previous cargo, lashing material, loose rust scale and paint flakes, etc. Prior to loading the holds must be swept, washed down with fresh water, dried and well ventilated. Light atmospheric rusting of exposed steel is generally acceptable but loose scale or paint, such that it may become detached and mix with the cargo, certainly is not.
“Normal Clean” requires the holds to be swept to remove all residues of the previous cargo, washed down and dried ready to receive a similar or compatible cargo.
“Shovel Clean” does not require washing but only the removal of the previous cargo by rough hand or mechanical sweeping.
It should however be noted that there is no universally accepted definition of these terms. Therefore, wherever possible, it is important to use as clear a description as possible when describing the cleaning standard required in a charterparty or voyage order.
A significant distinction in so far as hold cleanliness is the obligation that applies on delivery under charters and that which applies for intermediate hold cleaning. For a discussion on this issue see: 'Intermediate Hold Cleaning - Owners' Duty' and 'Hold Cleaning - Who Bears The Cost?'
Planning and Preparation for Hold Cleaning
To reduce the amount of hold cleaning required for the next cargo masters may utilise the discharge/cleaning facilities at the current port. By removing as much remnant of the prior cargo from the holds, disposal and clean-up costs can be reduced and time can be saved before the next load port. In order to effectively and quickly clean holds it is also important to have access to sufficient cleaning materials, including chemicals (if appropriate for the next cargo) and high pressure washing equipment on board.
When planning the hold cleaning operation the master should also properly assess the risks of this. For instance, if chemicals are to be used as part of the washing-down procedure, accurate data (MSDS) should be provided to the vessel to ensure the risks are understood and safe handling implemented. This will include a job specific risk assessment, a tool box talk and the correct use of personal protective equipment. Moreover, agreement on compatibility of the clean with the next intended cargo should be obtained from the shippers/charterers in order to ensure that there is clarity on the precise level of cleanliness they require the vessel to achieve, for example no loose rust, no bare steel or fully painted and cured.
With the introduction of new requirements under MARPOL Annex V, masters need to be aware that cargo residues, wash water and wash water containing chemicals which are Harmful to the Marine Environment (HME) must be identified as such and disposed of in the correct manner in order to avoid breaching these regulations (see 'MARPOL Annex V - Bulk Cargo Hold Wash Water Discharge and Cargo Declarations'.)
London Arbitration 4/17
Facts
The vessel was chartered out by disponent owners for the carriage of a bulk cargo of wheat.
Clause 77 of the Charterparty provided “Vessel’s holds on arrival load port to be clean, swept, dried up, free of loose paint/rust scale, free of cargo residues from previous voyage and in every respect ready to load the intended cargo to the satisfaction of the shipper’s independent surveyor. Should the vessel fail to pass the hold inspection, Owners to arrange cleaning at their time and expense.”
Four hold inspections were carried out, three of which the vessel passed and one which the vessel failed. These were as follows:
1. The first inspection was carried out on behalf of head owners at anchorage shortly after the vessel’s arrival, between 19.20 and 21.30, at which time it was dark. This report concluded that the holds were passed, without remark, and were ready for loading of grain cargo.
2. The second inspection was carried out on behalf of consignees, also at anchorage between 19.20 and 21.30. This report concluded that the holds were clean, dry, free from foreign smell, without residues of previous cargo and suitable for loading.
3. The third inspection was carried out by the loadport authorities after the vessel berthed between 0700 and 0800, at which time it was still dark. The report stated that the holds were clean and dry, without foreign smell and free from insects.
4. The fourth inspection, which failed the holds, was produced by an inspection team that included representatives of the authorities at the country of discharge, whose law required delegates to inspect and approve both the cargo to be imported and the carrying vessel. This inspection started at 07.10 and continued until 14.30 and found the presence of remnants of the previous cargo of coke and rust.
The master did not remark on the survey or issue any letter or protest in relation to the results of the fourth survey. However, he did instruct the crew to further clean the holds and this process took about three days.
Arguments and Decision
Owners suggested that the words “to grain clean standard” should be implied after the word “clean” in clause 77. However, the difficulty with this was that there was no uniform meaning to “grain clean standard” and the standard required by authorities around the world varied considerably. In these circumstances the tribunal concluded that this proposed implied term would not be workable.
Owners also argued that there should be a second implied term that the shippers would not appoint a “wholly ignorant or unreasonable inspector” who may unreasonably reject the vessel’s holds. While the tribunal agreed the clause 77 should not be used to require an unreasonable level of cleanliness this did not, however, mean that the standard required by the clause should be limited to those acceptable to the local authorities - particularly when those standards were at the lower end of the scale determined on a worldwide basis.
The tribunal commented that the first and second survey reports were superficial and far from convincing. They also remarked that it would be difficult to carry out a proper inspection at night in that time scale. So far as the third report was concerned, the tribunal also noted that it would not have been possible to visit each of the holds in that time scale and that it was dark at the time of the inspection.
As regards the fourth inspection, which failed the holds, it was held that as the shippers were contractually bound by this survey and as the inspectors were independent of the shippers, that this was an independent survey for the purpose of clause 77. It was also noted that this was the only survey which took place in the light and that it took significantly longer than any of the three preceding inspections, the implication being that this inspection was more thorough. Accordingly, the tribunal rejected Owner’s assertions that the inspection team was “wholly ignorant”, was not competent to carry out a survey and required an unreasonable standard of cleanliness. Instead, the tribunal interpreted the master’s decision to carry out cleaning as an acceptance that there were remnants of previous cargo and rust.
Despite the holds being passed by the first three inspectors, the tribunal accepted the findings of the fourth surveyor and concluded that there was presence of the rust and remnants of the previous cargo with the effect that the requirements of clause 77 were not met.
Comment
There are many different standards for hold cleaning, and how these are interpreted can vary widely depending on the port. In order to avoid delays, it is important to ensure that any charterparty provision is clear as to the standard required, for example where using a term such as grain clean that it is clearly stated what this is agreed to mean. It can also assist to include an agreement as to what steps are to be taken in the event that there is not a consensus on whether the holds are acceptable, for example appointment of a mutually acceptable surveyor as this can help with controlling any resulting delays.
It is also clear that surveyors can take very different approaches when inspecting the holds, from a cursory inspection to one which involves a careful inspection of all surfaces. In order to ensure that any challenge of an inspector’s finding can be limited, instructions should be given to the surveyor setting out the contractual requirements that the holds need to meet. If possible, it may also be useful for surveys to be coordinated so that the extent and timing of the surveys for each party are the same. If the findings of another surveyor are not agreed with, it is important that a timely protest is made.
Finally, some charterers have their own requirements, for example specific cleaning routines which are to be used prior to carriage of cargo. If this is the case, care should be taken to ensure any contractually agreed procedures are followed in order to reduce the scope for disputes.