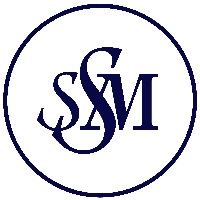
Steamship Mutual
Published: May 01, 2008
A recent spate of oil spills during routine bunkering operations has resulted in a number of significant pollution claims and has raised concerns as to the number of spillages resulting from a lapse of awareness during critical aspects of the bunkering operation or a basic failure to follow defined procedures. Empirical analysis shows that bunker fuel commonly escaped through the air vents of the bunker tanks. In most cases the quantities involved were substantial enough to breach savealls and plugged scuppers, resulting in escape of fuel from the confines of the vessel into the marine environment. The circumstances leading to each incident were often different. Bunker spills can of course also result where external factors impinge on the vessel’s operation. Notwithstanding external factors, the following were commonly identified as causative in the incidents reviewed:
- Failure to close completely a valve to a tank which had completed loading its nominated quantity of fuel. During filling of adjacent tanks, bunker fuel continued to enter the first completed tank unnoticed, eventually exceeding tank capacity;
- Failure to adhere to the stipulated maximum loading rate contained in the vessel’s bunker plan and agreed prior to operations. As a consequence of excessive rate of supply, air pockets collected in the top frames of the tank. When the fuel reached its optimum level in the tank, fuel was forcefully blown out through the air vents;
- Failure to adhere to recognised procedures for topping off tanks. During topping off a valve was closed against the flow of one of two receiving tanks. The flow rate was not reduced sufficiently and the increased pressure to the adjacent receiving tank resulted in overflow.
- Failure to monitor the progression of loading at adequate intervals resulting in overflow.
Bunkering is only one facet of a vessel’s dynamic operating schedule, but is categorised as a critical operation under the ISM Code1. Stemming bunkers commands careful planning, co-ordination and co-operation between all parties involved from the point of ordering until completion of the delivery. Commercial schedules can impose immense pressure on owners and a vessel’s crew to stem bunkers within limited time periods. However, non-compliance with recognised operating procedures in a vessel’s Safety Management System during bunker operations has the potential to result in substantial costs, penalties and even greater delay where spillage occurs as a consequence. In some jurisdictions accidental spillage of bunker fuel can also result in criminal charges. The ISM code requires companies to document and implement clear and detailed procedures, standards and instructions for safety management on board. It further requires companies to provide safe working practices and identify risks. Many companies incorporate the ISGOTT Bunkering Safety Checklist2 into their operations procedures, whilst some port authorities may insist on ISGOTT procedures being implemented. Checklists can serve to assist a vessel’s crew in undertaking the operation effectively, as long as diligence is exercised when undertaking the actual task. Blind compliance to checklists can only serve to reintroduce the attendant risks - in some incidents examined, checklists were marked as completed but the corresponding critical task not actually implemented. MARPOL Regulations3 govern the Prevention of Oil Pollution arising from oil pollution accidents. In particular, it is compulsory for ships of more than 400 Gross Tons (oil tankers over 150 GT) to carry a Shipboard Oil Pollution Emergency Plan (SOPEP) on board.4 The SOPEP conveys information from the owner to the Master on how to react in case of an oil spill. Actions to be taken within various scenarios as well as communications to be made to owner and other contact points are listed in a format required by the MARPOL Regulations. Many bunker spills are noticeably small in quantity. The resultant cost of deploying counter-pollution resources and undertaking substantial clean-up measures may appear disproportionate to the quantity spilled, though is nevertheless a distinctive feature of this type of claim. In a recent incident in Panama, a small spillage of around 2 MT of IFO spread rapidly along the adjacent coastal region, resulting in a six figure clean-up cost, two days delay to the vessel’s schedule and significant fines from the respective authorities. With the advent of the entry into force of the International Convention on Civil Liability for Bunker Oil Pollution Damage, 2001 (see Bunkers Convention in Force November 2008) and the potential for even more stringent action by other non-contracting states, shipowners will face even stricter regimes in liability compensation. From a loss prevention perspective, proper planning, continued vigilance and effective implementation of a recognised oil transfer procedure as part of a vessel’s Safety Management System are key components in ensuring that routine bunkering operations are completed safely and effectively, thus reducing the risk of harm to the marine environment.
1. Annex to the International Convention for the Safety of Life at Sea, 1974 (SOLAS) - Chapter IX: Management for the Safe Operation of Ships
2. ICS, OCIMF and IAPH, 2006, ISGOTT (5th Ed), 25.4.
3 Bunkering Safety Check-List, ISBN: 1 85609 291 3. MARPOL Annex I, Chapter 5
4. MARPOL Annex I, Chapter 5, Regulation 37