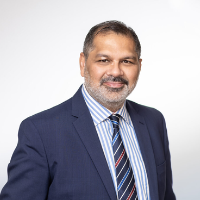
Taslim Imad
Published: April 03, 2025
Introduction:
In accordance with SOLAS Chapter VI Regulation 5: -
“cargoes shall be loaded, stowed and secured as to prevent as far as is practicable, throughout the voyage, damage or hazard to the ship and the persons on board, and loss of cargo overboard. Appropriate precautions shall be taken during loading and transport of heavy cargoes or cargoes with abnormal physical dimensions to ensure that no structural damage to the ship occurs and to maintain adequate stability throughout the voyage”.
The International Maritime Organisation (IMO) adopted IMO Assembly Resolution A.714(17) to provide an international standard to promote the safe stowage and securing of cargoes. As a result the Code of Safe Practice for Cargo Stowage and Securing (CSS Code) was introduced. The main principles of CSS Code are as follows –
- All cargoes should be stowed and secured in such a way that the ship and persons on board are not put at risk;
- The safe stowage and securing of cargoes depend on proper planning, execution and supervision;
- Personnel commissioned to tasks of cargo stowage and securing should be properly qualified and experienced;
- Personnel planning and supervising the stowage and securing of cargo should have a sound practical knowledge of the application and content of the Cargo Securing Manual
(CSM); - In all cases, improper stowage and securing of cargo will be potentially hazardous to the securing of other cargoes and to the ships itself;
- Decisions taken for measures of stowage and securing cargo should be based on the most severe weather conditions which may be expected by experience for the intended voyage; and
- Ship-handling decisions taken by the master, especially in bad weather conditions, should take into account the type and stowage position of the cargo and the securing arrangements.
Annex 6 and Annex 7 of the CSS Code are dedicated to coiled steel sheet and heavy metal products, however, it should be noted that these Annexes of the CSS Code, given their focus on cargo stowage and securing, do not fully consider all P&I related issues and the potential liabilities arising from the carriage of steel cargoes. For example, the CSS Code considers the structural aspect of the ship when carrying steel and heavy metal cargoes and the cargo securing arrangements, however it does not take into consideration P&I issues such as claims arising from ship sweat, cargo sweat, ingress of seawater or rain water, which can result in development of rust to the steel cargoes with consequential very large liability exposure. To examine the problems arising from the loading, carriage and discharging of steel cargoes a significant amount of research has been completed by industry experts and based on this research the Club would like to highlight some of the associated risks identified and provide guidance to its Members on damage prevention when loading, carrying and discharging steel cargoes.
Precautions:
Members should be aware that steel cargoes are very sensitive and expensive commodities, particularly finished steel products, and as such must be treated and carried with the utmost care and attention, if the risks of incurring large claims are to be minimised. Consequently, the Club generally recommends or may require steel shipments to be supervised by an experienced surveyor during cargo loading and discharging operations. In accordance with the principles of the CSS Code, all cargoes should be stowed and secured in such a way that the ship and persons on board are not put at risk. Therefore, the safe stowage and securing of steel cargoes depends on proper planning, execution and supervision by properly qualified and experienced personnel having a sound practical knowledge of the content of the vessel’s Cargo Securing Manual (CSM), the cargo holds, cargo stowage and cargo securing operations.
Stability, Maximum loads and Tank Top loading:
Ships are usually built under Class rules founded on the International Convention (SOLAS) and these produce the stability criteria and information that governs the carriage of different cargo types (e.g. grain, timber, steel, etc.). When a Shipowner orders a new ship, the builder will offer several designs to meet the requirements of trade, cost and delivery time. In accordance with SOLAS and the requirements of Flag Administration, Class is obliged to provide a book of calculations or a curve or table that illustrates the ship’s stability in various conditions of loading with various cargo types. The first pre-requisite in loading the ship, with any type of cargo, is that the designed loads must never be exceeded.
Whilst appearing obvious, it should be noted that steel cargoes are fundamentally heavy cargoes that produce cargo stows with a low centre of gravity. These commodities consequently exert high levels of stress on ship structures which may result in some limitations as to where these types of heavy cargoes can be loaded on a vessel. A general cargo vessel with tween decks may not be able to load heavy steel coils on her tween decks due to the weight of cargo in relation to the permissible designed load (t/m2) limitation, but steel tubes/pipes and similarly less dense steel cargoes may be capable of being loaded in such spaces.
However, on a bulk carrier there are no tween decks therefore any type of steel cargo on a bulk carrier and heavy steel coils on a general cargo vessel can only be loaded on tank tops. In contrast to a true bulk cargo such as grain where cargo holds will be substantially full when the ship is loaded to its full deadweight capacity, a full deadweight load of a steel cargo will be reached with much of the cargo holds empty. Consequently, the vertical centre of gravity of the cargo stow will be very low in the ship. This in turn results in a high figure for the “Metacentric Height” (GM). The GM is an important measure in relation to a vessel’s stability. When a vessel has a high GM it is referred to as being “stiff” in the context of its stability. If a ship is “stiff”, the “Righting Moment” (GZ) that is experienced when the vessel is heeled or inclined by external forces such as waves, swell or wind will return the ship back to her original upright position very quickly.
However, momentum resulting from the effect of the Righting Moment will result in the vessel then heeling or rolling past the vertical, thus initiating a rolling motion. It is to be noted that due to a large GZ, a ship with a high GM tends to roll with a shorter roll period even in moderate weather conditions. This motion will cause a vessel with steel cargo to be uncomfortable at sea, particularly during adverse weather conditions, and there is a risk that the vessel may stress herself and there may be consequential cargo shift and damage to the cargo, or to the vessel, as the result of the dynamic loads placed upon the cargo and its securing arrangements. The Master is advised to follow IMO Guidelines for avoiding dangerous situations in adverse weather and sea conditions and hence it is very important that where required additional lashings be applied to the cargo on a vessel with a very high GM.
When loading steel cargoes, pre-load and post load draught surveys are to be undertaken in order to determine the cargo quantity loaded on board. When a vessel reaches its maximum draught marks without exceeding the stress limitations then there are no issues. However, when a vessel is loading very dense and heavy steel coils or any other type of heavy steel cargoes, there is the potential for problems to arise when a vessel cannot reach its maximum draught marks due to the maximum permissible tank top loading having been achieved or where the longitudinal bending movements and shear forces exceed the safety limits of the vessel and this could lead to a dispute between the owners and charterers.
It should be noted that the objectives of the charterers or shippers, and the owners may not be aligned; the charterers or cargo interests wishing to load a complete deadweight cargo (down to maximum permitted draught) whilst the Master will need to ensure that the maximum tank top loads and other safety limitations are not exceeded and that the vessel remains safe at all times, there is the potential therefore for disputes.
In determining that the ship is not overloaded, it is therefore important to ensure that the designed maximum tank top load is not to be exceeded. This designed load is expressed in tonnes per square metre. Note that on bulk carriers the tank top area is often reduced by sloping hopper sides. There is no extra allowance made for hopper sides and this is not an area for compromise. When the maximum load has been determined this weight should be spread as evenly as possible across the tank top. It is also to be noted that most ships will have approved ship’s stability software on board which should enable optimisation of the maximum load without exceeding stresses on the ship beyond their permissible seagoing limits.
Types of steel cargoes:
There are many types of steel cargoes but from the Club’s experience, hot rolled sheeting (Coils), hot rolled sheeting (Bundles), cold rolled sheeting (Coils), cold rolled sheeting (Packs), wire rods, structural steel, galvanised steel and tin plate are the main types of steel cargoes that may result in large claims. Other steel cargoes include steel billets, steel blooms, steel scrap and pig iron.
Packaged steel cargoes:
Steel cargoes which are finished products generally come wrapped in metal envelopes and are ready for direct use without further processing i.e. cold rolled steel sheeting, and therefore must be handled and transported with extreme care to avoid expensive claims. Hot rolled steel cargoes which would require further processing like unwrapped steel sheeting (in coils or bundles), constructional steel, reinforcing bars and wire rods, whilst being somewhat less sensitive, are still cargoes that can be harmed significantly by seawater, rain water and unsatisfactory stowage or careless handling.
Importance of engaging an independent cargo surveyor:
Steel cargoes are water sensitive, liable to damage and with the potential for large claims and, whilst the ship staff have a duty of care and responsibility for the cargo the Club recommends, and would like to stress the importance, of appointing an independent cargo surveyor to protect the Member’s interests when loading hot rolled steel in coils or bundles, cold rolled steel in coils, packs or bundles, galvanised steel, stainless steel, tin plate, wire rods, steel pipes and structural steel (rebars, channels, angles, beams, bars, strips, sections, forgings). The independent surveyor should: –
- Check and verify the condition of the steel cargo lying at port premises before being loaded onboard the Member’s vessel;
- Verify that the hatch covers, their associated fittings and other related openings are in sound condition and carry out an ultrasonic test (UST) of the cargo hold hatch covers and related items. As evidence, supporting photographs are to be taken documenting the condition of the hatch covers, rubber packing and associated items and these must be retained for future reference in the event of a claim;
- Check cargo holds are properly prepared (Swept and free from residue of previous cargo, loose rust and paint flakes, thoroughly washed down with fresh water, completely dry and that there are no signs of salt or sea or rain water) and as evidence take appropriate supporting photographs for every cargo hold prior to the loading operation;
- Check and verify that cargo hold bilges and bilge wells have been dried out, bilge cover plates and strum boxes must be cleared, cleaned and secured. A suction test of the bilges, including a pressure test of nonreturn valves is to be carried out prior to the loading operation. Ensure that there is no drop in suction from bilge discharge and that the non-return valve is not faulty avoiding the potential for back flow of water from bilge line/s to the cargo hold/s with consequential damage of steel cargo during the voyage. As evidence appropriate documentary records with accompanying supporting photographs should be taken.
- Ensure that the manhole covers of any tanks, fuel oil, ballast etc within the cargo holds/ spaces are properly secured, tightened and pressure tested to avoid any potential leakages/ hold flooding with resulting damage to the steel cargo.
- Ensure permissible weight on ship’s cargo hold tank top is not exceeded at any time as this could result in damage to the ship’s structure;
- Record any damage to the ship’s structure caused by the cargo operation, this is to be noted and immediately advised to all concern stakeholders and as evidence adequate numbers of supporting photograph are to be taken;
- Ensure sufficient and appropriate dunnage, correctly applied, for the cargo being carried. Three lines of 15cm x 4cm dunnage would be acceptable, however the precise nature and quantity of dunnage that should be used will be a matter for discussion between the Master and Shipper/Charterer taking into account factors such as the weight, size, footprint and other applicable characteristics of the cargo being loaded, with due account and consideration to the age of the ship and the physical condition of ship’s deck (tank top);
- Ensure suitable, sufficient number, appropriately sized and rigged strong lashings are applied to the cargo, correctly secured in line with the minimum requirements of the approved CSM. When determining final lashing arrangements, Metacentric height (GM) and the potential for adverse weather condition during the course of upcoming voyage need to be taken into consideration;
- Ensure, where possible, that there is no direct steel to steel contact;
- Assist with monitoring the loading / stowage / securing of the steel cargo
- Assist Masters and officers in recording the apparent condition of the cargo so that, where appropriate, mate’s receipts and bills of lading can be claused correctly; and
- When the steel cargo is damaged by the mishandling of stevedores support the damaged cargo being removed from the
ship if possible. If it is not possible to replace damaged cargo with sound, prepare correct damage report/s and support the master to issue a correct “Note of Protest” (NOP) and if appropriate in clausing mate’s receipts and bills of lading correctly in order to protect the Member’s interests.
The steel cargoes of a less sensitive nature and some semi-finished materials may not require the attendance of a surveyor, for example steel billets, steel blooms, steel scrap and pig iron.
Preparation of cargo holds:
Most disputes and claims with steel cargoes arise at the discharging port with rust related issues. The receivers of steel cargoes will always expect carriers to be responsible and accountable for the weathertight integrity of the cargo holds and their hatch covers of the ship on which steel cargoes are carried. More is required than just compliance with the statutory requirements of the International Convention on Load Lines, 1996 as amended to establish the seaworthiness of ships and their cargo holds. In accordance with Article III of the Hague-Visby rules, “there is an obligation on the Carrier to exercise due diligence before and at the beginning of the voyage to make the ship seaworthy and make the cargo holds, and all other parts of the ship in which goods are carried, “fit and safe for their reception, carriage and preservation”. This point is reiterated in Article IV of the Hague-Visby rules, “Neither the Carrier nor the ship shall be liable for loss or damage arising or resulting from unseaworthiness unless caused by want of due diligence on the part of the Carrier to make the ship seaworthy”, therefore, to avoid sea water ingress and unseaworthiness claims a test of a good hatch cover sealing arrangement at the beginning of the voyage is very important to protect the cargo by preventing the ingress of rain and sea water into the cargo holds and maintaining weathertight integrity of the cargo holds in all sea states.