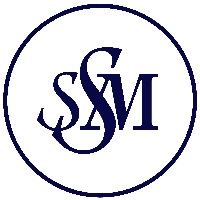
Steamship Mutual
Published: March 01, 2009
The Club is increasingly coming across cases where cargo has shifted or broken free from its lashings due to the incorrect use and fitting of wire securing clips, also known as bulldog grips when making up wire rope eye terminations. These are either not being correctly fitted by lashing gangs or ships crews, or items are being presented for shipment on flat rack containers where the improper use of wire rope clips means the lashings between cargo and container are not fit for purpose.
When making an eye termination in a wire rope using wire rope clips the eye can either be a hard eye utilising a thimble, which is the preferred method, or a soft eye with the wire just looped and turned back on itself. The amount of wire to be turned back depends on the wire diameter and is measured from the throat of the eye, not the eye extremity. It must be ensured that the wire clips used are suitable for the diameter of the wire being terminated and the number of clips required is dependent on the diameter of the wire used.
The first clip is applied at the dead end of the turned back wire, one saddle length from the extremity of the seized wire end. One of the most common mistakes when eye terminations are made is that the wire clip is applied the wrong way around; the U bolt must be over the dead part of the wire and the saddle on the live or load bearing part. The mnemonic best used to remember how to apply the wire clip is "Never Saddle A Dead Horse" i.e., the saddle of the wire clip is never fitted to the dead part of the wire, this is so that the live or load bearing part of the wire is not subject to crush damage by the U bolt. Once the saddle is fitted over the U bolt the nuts should be tightened evenly alternating from one nut to the other. These two nuts should be tightened to the recommended torque for the size of wire clip being used in line with the manufacturers’ guidelines. The second wire clip should then be placed as close to the throat of the eye or thimble as is possible, but not such that it is binding on the thimble. If only two wire clips are necessary then the nuts on this clip should be tightened evenly alternating from one nut to the other to the recommended torque. If more than two wire clips are to be used then the nuts on the second clip at the eye throat should only be hand tightened at this stage. When there are three or more clips required the remaining clips are to be placed at equidistant intervals between the first two. Once all the remaining wire clips are fitted and the nuts have been hand tightened, the nuts on the second clip at the eye throat and on the remaining clips can be tightened to the required torque.
The preferred method of joining two wires together using wire clips is to join two eyes ‘back to back’. It is not recommended that two wires are joined directly to one another, but when the dead end of two wire ropes are joined together the overlap between the parallel wires must be twice the turn back length specified for the size of wire being joined. The number of wire clips will again depend on the diameter of the wire, and these are to be fitted such that the live/load bearing part of the wire within the first turn back length will be considered live and the saddles will be fitted on the live/load bearing part of the wire and the U bolt over the dead end of the second wire, the second turn back length leading to the seized end of the wire will be considered the dead end and as such the U bolts of the wire clips in this length will sit on this part of the wire. The result will be that the wire clips within the two different halves of the join will be opposing each other. The first wire clip at each end of the join will, as for the eye termination, be one saddle length from the dead end of the wire, and those wire clips in between are to be equidistantly placed. The tightening torque will again be in line with the wire clip manufacturers’ guidelines.
Information on the size of clip to use, the turn back length required, number of clips to use and the nut tightening torque can be obtained from wire clip manufactures.
In line with normal best practice all such terminations and joins should be checked after load has been applied as tension in the wire may make the nuts become loose. Thereafter the lashing should be periodically checked for wear, damage and integrity, and the nuts kept torqued to the recommended tightness.
It is generally accepted that a wire clip termination will, if properly constructed and maintained, have an efficiency factor of 0.8 of the breaking strength of the wire rope being used.