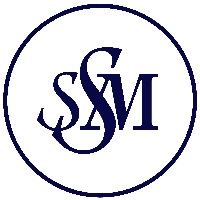
Steamship Mutual
Published: August 09, 2010
December 2004
The annual claims analysis undertaken by the Club continues to feature leaking hatchcovers as a cause of major cargo claims. Also many smaller claims continue to arise from the same cause. Water ingress is often the result of poor maintenance of hatch covers and coamings, or the failure to secure hatchcovers effectively.
One of the key areas for loss prevention in the scope of the Club's Condition Surveys is the testing of hatch covers for watertight integrity. The most common methods of leak detection are water hose test and ultrasonic test. Although both methods are widely used, ultrasonic testing when the necessary equipment is available, is the Club's preferred method. Often difficulties are encountered in explaining why the ultrasonic test is considered to be a more reliable indicator of the watertight integrity of hatch covers than a hose test. This article reviews the two methods.
Hose Tests
The ability of the most commonly used hatch covers to prevent water ingress depends upon the existence of a watertight seal between sections of rubber packing and steel compression bars. A hose test involves playing a jet of water along the cross joints and perimeter seals of the hatch covers at a certain minimum pressure and distance from the structure. It requires a minimum of two people to carry it out. One to operate the hose and one to observe from within the hold to see whether water is gaining access. If no water is seen to enter the hold, what the test is demonstrating is the existence of "contact" between the steel compression bars and the rubber packing. However, it should be noted, that a lack of leakage into the hold is not of itself determinative of a successful test. Checks should also be made that leakage is not passing into the drain channels and being fed through the drain valves onto the deck.
- Hose testing will discover hatchcover joints that leak. However, the method has its limitations:
- Cargo holds must be free of cargo
- The test is not viable in sub-zero temperatures
- The test cannot pinpoint leakages accurately
- Water pressure variance and the distance of the jet from the structure can affect results
- Many port authorities will not permit it because excess water on deck can lead to pollution
- A minimum of two ship's crew is required
Further, hose tests are always conducted in static conditions. When the ship is at sea, the ship itself and its hatch and coaming structures are not completely rigid. They flex and "work" to cope with the forces to which they are subjected by the ship's motion and the forces of wind and waves. If cargo damage is to be avoided, the contact between the compression bars and the rubber packing has to be maintained during the periods when the covers and coamings are flexing. The extent to which that contact is maintained depends upon the degree of "compression" that is being achieved by the steel to rubber contact. The higher the degree of compression, the greater will be the watertight integrity in dynamic conditions. A hose test can only demonstrate "contact" not "compression". It is this shortcoming that it makes it a considerably less reliable indicator of overall watertightness than the ultrasonic test.
Ultrasonic Tests
The use of ultrasonic equipment is a modern, viable means of testing for watertight integrity of hatchcovers, access hatches, doors, ventilators, etc. It is preferable to use Class approved equipment operated by qualified personnel and to follow approved test procedures.
The test involves placing an electronic signal generator within the cargo hold (laden or not) and using the receiving sensor to first take a reading at the access or booby hatch with the main hatchcover closed. This provides the OHV (open hatch value). The sensor is then passed around the outside of all compression joints noting the reading on the receiving equipment. It is preferable to listen to the signal using headphones to determine the maximum reading at any single point. The readings obtained are then compared with the OHV. The closer they are to the OHV, the greater the degree of leakage. The comparison between actual readings and OHV indicates the degree of compression that exists within the seal, the greater the compression, the lower the reading as a percentage of the OHV. For this reason the ultrasonic test is a much more reliable indicator of watertight integrity in dynamic conditions.
For the purpose of evaluation of results, the following guidelines are usually adopted:
- Readings of 50% of the OHV or more indicate significant loss of compression and an immediate lack of watertight integrity.
- Readings of more than 10% indicate potential leakage.
- Readings of less than 10% indicate weathertightness under normal conditions.
A further advantage of ultrasonic testing is that none of the limitations of hose testing apply to this method. The ability to conduct the test with the holds laden is a particular benefit.
Ultrasonic testing will enable the location of leaks to be pinpointed quickly and accurately. After the test, it is imperative to conduct a visual inspection to determine the reason for leakage and thereby determine the appropriate remedial action.