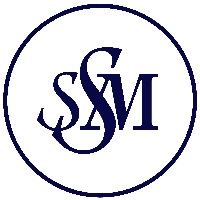
Steamship Mutual
Published: August 09, 2010
March 2000
INTRODUCTION
There is arguably nothing new about fuel oil quantity and quality problems on board ship; they are almost a daily occurrence for ship owners/managers and Chief Engineers alike. Short periods in port make it practically impossible to verify the quality of bunkers delivered before the ship has to sail. Prudent owners use fuel analysis services such as those provided by Det Norske Veritas Petroleum Services (DNVPS) and Lloyd's Fuel Oil Bunker Analysis Service (FOBAS). Even so, the results of such analysis can take between 3 and 10 days to reach the ship operator. The time depends largely on where the sample is landed and whether the agent remembers it is in his car boot. In the meantime, the new fuel needs to be segregated onboard and cannot be used without risk of damage to the main and possibly auxiliary engines. In short, the buyer performs a leap of faith every time his ship is fuelled.
Advice regarding bunkering procedure, sampling techniques and fuel specification standards is plentiful and generally well known throughout the industry. When problems do occur it is the ship's engineers who initially face the inconvenience and who are required to resolve whatever difficulty has arisen in short time. It is in everyone's best interests to find a solution quickly to prevent the vessel being delayed or put at risk.
This article draws on the author's experience as a Chief Engineer, Superintendent, Fleet Manager and surveyor; it seeks to identify some of the more common quality and quantity problems that occur onboard during the normal course of events and provide some practical guidance to assist the ship's engineer in determining an appropriate course of action. It is not exhaustive, and deliberately avoids issues which receive a more regular airing; such as fuel specification and process equipment operation.
THE BUNKERING PROCESS
Much has been written about the importance of taking representative samples of fuel during the bunkering process, all of which is to be recommended. Such procedures are well documented and it is not the intention to re-cover this ground here.
Nevertheless, it is as well to be aware of one particular shortfall in the "continuous drip" method of sampling. The most common form of shipboard bunker sampling during fuelling is the "continuous drip". A small diameter tube, inserted into the bunker pipeline at the ship's manifold (commonly referred to as the custody transfer point), provides a sample of fuel during the bunker period. The rate of sampling is controlled by a needle valve at one end of the tube, which is normally regulated to drip into a sealed plastic container.
The Problem
Residual fuels are almost always cut back with distillate stock to obtain the required/ordered viscosity. Refineries keep only limited stocks of pre-prepared bunker fuels, preferring to mix to order when required. Often the process of blending the residuum with the cutter stock is carried out on the bunker barge and may, for a number of reasons, not occur satisfactorily. The result may be that a product of wholly different characteristics is loaded into a vessel over distinctly separate periods of the bunker transfer. If the vessel has relatively small oil storage tanks, as is common in some vessel types, the fuel loaded into these tanks may differ significantly with regard to its constituent parts. The "continuous drip" sample, diligently collected over the entire bunkering process will, however, contain the correct proportions of the fuel blend components and show nothing untoward.
The Solution
Blending of fuels in this manner is not "rocket science"; it consists of little more than gradually introducing the cutter stock whilst pumping the components around in the bunker tanks until thorough mixing has occurred. If inadequate blending is suspected and this might be evidenced by sudden changes in the sample flow, say from a drip to a stream, whilst at constant temperature, bunkering should be stopped. Simple viscosity comparisons can be quickly carried out between oil from different tanks on the bunker barge to check for uniformity. Viscosity differences in a poorly blended fuel will usually be readily apparent.
If fuel transfer has been completed before a problem with blending comes to light and, providing subsequent sample analysis results prove satisfactory, the problem may be solved by pumping the fuel around the vessel to aid the mixing process. In some cases, where the cutter stock has been short delivered, it may be possible to add this at a later stage onboard. Blending charts are available to ascertain the appropriate addition of distillate for the desired viscosity. A word of warning though, this should never be attempted without first consulting the supplier and seeking an independent view from an organisation such as FOBAS or DNVPS. It would be essential to establish that the blending components are compatible and will not cause instability when mixed.
DISTILLATE FUEL
The Problem
Occasionally, an analysis result for diesel or gas oils bunkered on a vessel will indicate a lower than permitted flash-point temperature. With the exception of pure distillate fuels, required for use in emergency engines, external to the machinery spaces, the flash point should be no lower than 600C (430C for DMX fuels).
In most cases the fuel will need to be pumped off the vessel at the earliest opportunity and replaced with fuel of the correct specification. Whilst the fuel remains on the ship it must not be used and should be segregated. The provision of No Smoking areas in the region of storage tank vents should be considered as mandatory.
The Solution
It is seldom possible to off-load the subject fuel quickly. The vessel will have sailed before receiving the analysis results and may not reach a port with adequate facilities for some days or even weeks. It has been known in borderline cases (550C to 590C) for the flash point to increase by a few degrees over time, particularly when the vessel is operating in warmer climates. This happens because the lighter ends of the fuel evaporate, thus increasing the flash point temperature. It is worthwhile, therefore, to perform a further flash point test before finally off loading the fuel, as this may eliminate the need for costly and time consuming pumping operations. A negotiated settlement with the oil supplier, taking into account the reasonable out of pocket expenses incurred by the ship owner, is likely to follow without too much difficulty. After all, the supplier will be very relieved that he did not have to foot the bill for re-supply and management of the out of spec fuel.
QUANTITY
The Problem
Those among us who have sailed on tankers with large uniformly shaped fuel storage tanks can probably boast that bunker barge outturn figures matched the ship's calculated received volume more or less exactly. More often than not though there is a difference, which invariably puts pressure on the Chief Engineer. He must of course protect his position but will be loathe to put in motion a sequence of events that may delay the vessel and give rise to significant costs. The temptation to accuse the bunker barge of having inaccurate tank calibration tables is strong, but before going down that route, which is difficult and costly to prove, it may be wise to consider the following.
Vessels of numerous, relatively small bunker storage tanks, of irregular shape, including shell curvatures, are not easily calibrated. As a result, there may be inaccuracies in the ship's own calibration tables, particularly if the vessel is not on an even keel.
The Solution
The Chief Engineer can be more confident of his protest against the barge and add more weight to his argument if he can produce documentary evidence from past bunkering operations. Previous bunkering particulars, including the quantities of oil received (ship's calculation) and notified barge outturn figures are very useful. This historical bunker information can be used to calculate an average "error" or "experience" factor for the vessel at its common bunker ports. The more data collected, the more accurate will be the "experience factor".
For example, if a vessel has recorded the last five bunkering particulars for Singapore, all of which had been at even keel, the results might be something like those shown below.
DATE 1/1980 2/1980 3/1980 4/1980 5/1980 PORT S'pore S'pore S'pore S'pore S'pore SHIP TRIM E/K E/K E/K E/K E/K SHIP LIST Nil Nil Nil Nil Nil LOADED TKS 5p/5s 5p/5s 5p/5s 5p/5s 5p/5s GRADE OF FUEL 380 380 380 380 380 BARGE NAME Con1 Con2 Con1 Con3 Con2 RCVD VOLUME 750 350 770 300 735 BARGE OUTTURN 780 365 810 330 750A trend can clearly be seen in the bunker figures over these five months. It is apparent that the ship always receives less than the barge outturn. When the vessel bunkers at Singapore on an even keel the "experience factor" is as follows.
750+350+770+300+735
= 2905/3035 = 0.957 780+ 365+810+330+750The Chief Engineer can reasonably assume that, for this vessel, the received fuel quantity (as calculated onboard) is likely to be 96% of the reported barge outturn. This factor may alter when the vessel is not on an even keel.
If the received measured volume is outside the "experience factor", further investigation is warranted. The Chief Engineer ought to personally supervise a further set of ullages from both the barge tanks and the ship. If he is still unable to reconcile the figures he should place the supplier on notice. If the difference is significant, an independent surveyor should be called to carry out a detailed investigation. This historical information can be available to any Chief Engineer serving on this vessel and provides a yardstick by which he can gauge his response.
QUALITY
The prudent ship operator will routinely have bunker supplies analysed. Providing the bunkers are not used before analysis results have been received, major damage to engine components, through poor quality fuels will be avoided.
The Problem
Fuel problems may nevertheless still occur in some circumstances. As it is not always possible to load fuel into empty tanks, particularly when the Chief Engineer is required to "bunker to capacity" (max 97%), some mixing with previous bunker fuels may be inevitable. The practice is not condoned here, but we all live in the real world and it is as well to appreciate the consequences of such actions, as they undoubtedly occur.
The Solution
As a result of admixing the fuel may become unstable, that is, it may begin to chemically fall apart. Typically, increased amounts of asphaltenic sludge will be noted in the fuel. An onboard test method is available to confirm whether two fuels are compatible, however, it is not particularly reliable as free oil insoluble contaminants in the sample may produce false results. Nevertheless, it provides an indication of compatibility. Equal quantities of the oils are mixed thoroughly at an elevated temperature (usually 1000C). A drop of the sample mixture is placed on a piece of chromotographic paper, which is then allowed to dry. The pattern produced by the droplet is then compared to five reference spots. The appearance of any deposit or ring will indicate a potentially unsatisfactory fuel blend. Although the results cannot be viewed as entirely conclusive they do offer a degree of comfort if admixing was unavoidable or warning of potential difficulties to come.
The Problem
If a problem occurs with mixed bunkers it is likely to be first noticed at the purifier. Excessive discharge of a "mousse" like sludge from the purifier is a common indication. When this stage is reached it is unlikely that the purifier will operate satisfactorily. Time is now of the essence, as the level in the fuel oil service tank cannot be maintained with the purifier off.
The Solution
A number of options are open to the engineers. It may be possible to drain the settling tank back into the bunker tank from which the oil originated (ships with gravity bunker systems), then fresh oil from a tank where admixing has not occurred can be pumped up to the settling tank. It may also be possible to slow the purifier throughput sufficiently to maintain a seal whilst still discharging processed fuel. In this case the vessel speed will have to be drastically reduced to match consumption to purifier output. In the most extreme case, the vessel may need to change over to diesel fuel (if she carries it) and proceed to the nearest port/anchorage for assistance. This is arguably one of the most difficult operational decisions a Chief Engineer could be faced with. If in his view, the heavy bunker fuel is unusable and there is sufficient diesel oil to reach a safe port, this must be his advice to the Master. No one will thank him if tugs have to be arranged to tow the vessel and the main engine has been damaged through use with unprocessed fuel oil.
SEDIMENT
Residual fuel can simply be defined as that which is left behind after distillation. The increased efficiency of refinery processes has led to a higher concentration of the poorer quality components in residual fuels. Blending residuum with various "cutter stocks", as previously described, to obtain a specified viscosity, produces bunker fuels used on ships.
The Problem
All bunker fuels contain some sediment, commonly in the form of carbonaceous material, catalytic fines, sand, dirt, rust etc. Under normal circumstances the degree of solid contaminants can be dealt with satisfactorily through the fuel processing plant, purifiers, filters etc. However, this sediment can, over a period of years, accumulate in the double bottom and settling fuel oil storage tanks.
The degree to which sediment accumulates depends largely on fuel quality and a particular ship's seakeeping characteristics. The poorer the fuel quality is in terms of solid contaminants, the greater will be the potential for precipitation to occur. A vessel that pitches and rolls significantly is more likely to agitate the bunker fuel and keep more of the contaminants within the body of the fuel. A large vessel that moves ponderously will not agitate the mixture sufficiently, thus allowing larger amounts of sediment to accumulate on the tank floor.
After time a layer of sediment will form on the tank bottom and horizontal frame surfaces. It causes no operational problem because the ship's normal movement is insufficient to disturb it. In fact it has been able to accumulate in spite of the ship's typical rolling and pitching movements. It is only when the vessel moves more violently than normal, perhaps in severe adverse weather that the sediment becomes disturbed and mixes with the oil.
When oil is next transferred from the bunker tank to the settling tank (typically twice per day), it will contain abnormally high levels of solid contaminants. The fuel process system is likely to be overwhelmed. Purifiers/Clarifiers will not be able to sufficiently reduce the solid material in the fuel, which will then pass to the service tank and final filters before the main engine fuel pumps. These filters will become blocked ever more frequently. If the filters are not in good condition and fuel is allowed to flow onwards, serious damage will result to the fuel pumps, fuel injectors, pistons and liners.
The Solution
The importance of monitoring the fuel process system cannot be overstressed. If it is noted that purification is more troublesome during or immediately after adverse weather or fuel filter cleaning/change-over becomes more frequent, sediment accumulation should be suspected. Tanks should be investigated and cleaned as necessary at the earliest opportunity. In any event a prudent ship operator will ensure that settling and service tanks are cleaned at every dry docking. The condition of bunker tanks should also be closely monitored.
Cleaning of tanks, particularly double bottom tanks, is costly and time consuming. However, it should be borne in mind that it is not necessary to "polish" the tanks they need only be de-sludged.
A FINAL WORD
Although some scope exists to rectify fuel problems onboard, it is limited. There is no room for any misunderstandings about fuel specification requirements between the ship operator and charterer/supplier. The standard of fuel received and the quality of its treatment onboard before use in the main machinery is crucial. Engine maintenance costs and vessel operating reliability are directly proportional to the fuel condition. The reconditioning/renewal expenses associated with main and auxiliary engine fuel injection, piston, liner and cylinder head equipment forms a substantial part of any annual machinery budget. Small improvements in the fuel quality produce remarkable reductions in maintenance frequency and consequent financial benefits.
With thanks to Stephen R. Knapp IEng AMIMarE of Con-Mar International Ltd for preparing this article
See related article: "Test kits for Marine Bunkers (INTERTANKO)"